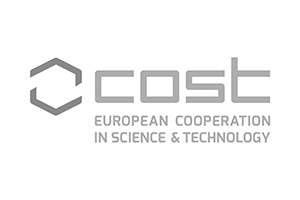
The main objective of the Action is to develop an innovative ‘integrated toolbox’ of predictive methods/models and targeted invasive and non-invasive measurement techniques, improving the means for European industries to reliably quantify the condition and remaining life of plant components in all types of conventional fossil, biomass and waste-fired power plant.
The specific objectives of this Action are summarised as follows:
- To provide reliable techniques for both on-line and off-line feedback of data on the condition of the critical components and the operating environment.
- To develop novel, accurate and validated life prediction methods, models and tools.
- To integrate the component condition feedback with newly developed models to provide an accurate diagnostic set of tools to predict the remnant life of critical plant components.
The key deliverable, the integrated toolbox, which is illustrated in Figure 1 with its associated drivers, not only allows improved assessment of component remnant lives but will also provide on-going intermittent and/or continuous monitoring techniques, means of assessing the risks of operational/fuel changes and feedback to improve the design methods employed on future plant.
As alluded to above, existing methodologies for PLE, although widely practised, are difficult to implement effectively and can be unreliable because they fail to include all the necessary factors and mechanisms influencing component failures. A key focus of the Action will therefore be the interfaces between the microstructural, environmental and mechanical modelling elements of the toolbox. The COST Action will enable a balanced multi-disciplinary skill-base to address this challenge and provide the overall integration of the modelling and measurement tools.
In order to meet the diverse demands of different types of fossil and associated biomass, waste and co-fired power plant, the predictive methods/models will comprise elements structured to deal with the primary failure modes (creep, fatigue, oxidation, corrosion, etc.) appropriate to the key components identified by the industrial partners. In addition, the materials selected for the development of the methods/models will be chosen as generic examples of those either currently in service or likely to be used in replacement parts in existing plant in the near future. Typical materials may include: for gas turbines, blading alloys such as CMSX-4 and IN738LC (with and without thermal barrier coatings (TBCs) and/or corrosion resistant coatings); for boilers/steam systems, P91, AISI 316L and 0.5CrMoV steels.
The benefits to industry will include: more accurate component lifetime predictions; reduced plant outage; increased service intervals; and access to better, cheaper life prediction tools, leading to an improved design capability for any new plant.
Additionally, for the worldwide electricity market, the life extension of conventional power plants with increased efficiency/reduced emissions will provide low cost electricity while the advanced low-CO2 emission fossil fuel plants and renewable options are being developed and implemented, thus avoiding the damaging effects of high energy prices on EU wealth creation over that period. European based utility and manufacturing companies will also be able to implement improved PLE techniques in their businesses worldwide.
Koordinatorius: Cranfield universitetas, Jungtinė Karalystė
Projekto vykdytojai
Vardas, pavardė | kabinetas | tel. nr. | el. paštas |
---|---|---|---|
Instituto atstovas |
|||
Rimantas Levinskas | 122-AK | +37037401804 | Rimantas.Levinskas@lei.lt |
Projekto vykdytojai |
|||
Arūnas Baltušnikas | 136-LK | +37037401906 | Arunas.Baltusnikas@lei.lt |